While many hope for the new year to deliver better income and opportunities, owner-operators contend with no small number of challenges at mid-Winter. This time of year, weather and road conditions generally become a principal focus -- that is, until something worse interrupts daily planning.
How big a problem seems depends on many factors. Throughout last year, problems like parts sourcing and service delays, which would normally rank as smaller problems for many owners, have been multiplying, like snowfall building layer upon layer until an avalanche is inevitable.
Beginning last Fall, discussions surrounding the supply chain disruptions for truck parts and preventive maintenance service supplies, such as oil and those filters, began to build steam after signs early in the year that it could get worse. Some people heard the warnings and began stocking up with inventory for these normally readily available supplies.
[Related: Parts delays appear to be the rule for major service/repairs in 2021]
Yet at the end of the first week of the new year, I received a message from an owner indicating he was sitting at one of the nation’s largest truck stops and there was no oil for his routine service. Granted, he was looking for a synthetic 5W40, and other, more conventional oil types were available. But a quick canvass of the region around where he sat yielded much the same – nothing available. I have been doing some Internet searching as of late, and some companies indicate it may be 30 plus days until they receive products that are short, whether oil or something else.
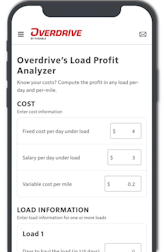
Given these dynamics, new truck manufacturing interruptions, more miles on current equipment and so much more, there’s a definite repair and maintenance backlog for lots of owners. The high cost of downtime can easily overwhelm an owner-operator’s ability to meet business and personal needs.
When it comes to oil, consider these mitigation strategies.
- Get into the practice of having your motor oil sampled and tested first before changing the oil. Many owners even of newer trucks with longer recommended oil-change intervals continue to stick to tried-and-true 15,000-mile intervals, sometimes even shorter. With sampling, and recommended filter changes as the case may be, these intervals might be extended greatly, depending on the engine and filtration in place.
- If you encounter a spot outage, consider having your oil filter changed even if the shop cannot completely change all the oil.
- Evaluate your options for adjusting your miles and schedule to allow time to locate and purchase oil and filters.
- Is this the time to install an oil by-pass filter system? That also may allow extending the intervals for the complete oil change, depending on your truck.
Owner-operator David Nihart of Wilmington, Ohio, uses the OPS bypass filter system with his 2007 Cummins ISX CM-870. The truck has 870,000 miles on the odometer. He currently samples and test engine oil every 25,000 miles. He historically changes every 50,000 miles, based on soot levels.
OPS is now a Pittsburg Power product. Estimated system cost is around $860. Sample kits, filters and oil per service looks to be $130-$150 depending on the size of the filter. An advantage is that changing the filter requires just a minimum of oil, about half a gallon. To learn more, you can access information through this link.
[Related: Glen Rice’s 2007 big-bunk W900 and savings from next-gen oil bypass, fuel treatment]
Don’t ignore other maintenance.
It’s easy to get upset when normally routine service is held up by a lack of something as simple as oil or an oil filter. Yet don’t just turn and stomp out the door – remember other maintenance needs:
- Greasing trucks and trailers may be one of the best investments you could make to help avoid more costly repairs, especially in winter.
- Inspection of the entire brake system and replacement of worn or damaged parts. Rust jacking can be a common issue this time of year.
- Load test batteries and clean terminals and the ground-to-frame connections from the batteries and the starter.
- Inspection of belts, hoses and coolant, and a test of your charge air cooler system, may help prevent a costly roadside breakdown.
It likely took a long time to get into whatever difficulty you may be experiencing. I suggest for many problems it may take an equal amount of time to reverse the course. Start by prioritizing decisions to fully address needs.
This simple daily management procedure is 100 years old, and proven to be effective -- the Ivy Lee method.
- At the end of each workday, write down the six most important things you need to accomplish tomorrow. Do not write down more than six tasks.
- Prioritize those six items in order of true importance.
- The next day, first concentrate only on the first task. Work until the first task is finished before moving on to the second task.
- Approach the rest of your list in the same fashion. At the end of the day, move any unfinished items to a new list of six tasks for the following day.
- Repeat this process every working day.
Supply chain shortages have been good for the demand for drivers and trucks, pushing spot rates to historically high levels. Yet at the same time, these dynamics push the cost of operating higher with inflation and all those trucking-related shortages. Yet despite these issues, the owners I assist (and business service firm ATBS's benchmark indicators) still point to generally higher net profits for 2021. The mood among Overdrive readers looking out at 2022 is upbeat in comparison to many prior years, with a majority of owner-operators expecting either better or at least equal income compared to 2021.
As an individual owner, will you just maintain profitability – or could you improve?
[Related: Per-diem tax breaks just got a lot simpler -- and more valuable -- for owner-operators]